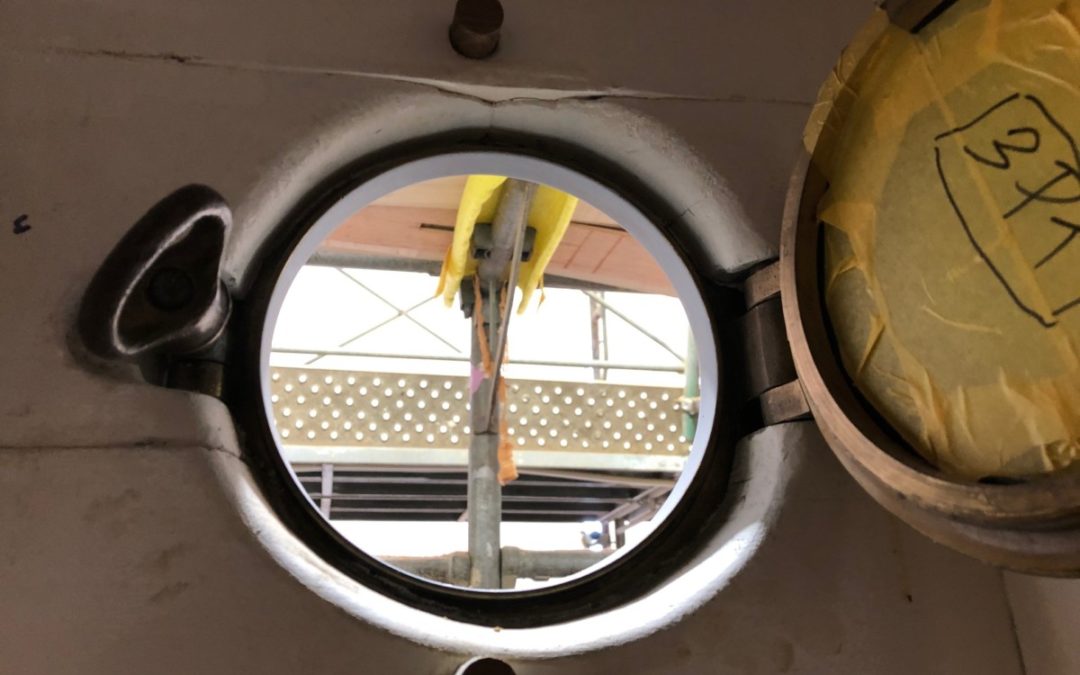
Blog — Friday, 27 December, 2019
Work on Cynara did not slow down at year-end, unlike the rest of Japan.
On Monday, Graham was working on attaching the copper sheathing to sections of the rudder. He carefully made thick paper templates of each piece then cut these shapes out of copper sheets. A heater was used to melt the pitch into which the copper is bedded.
In the old days, copper was used to sheath the underwater hulls of ships to protect them from corrosion, worms and barnacles. The practice started with the Royal Navy and spread to the wealthier merchants’ ships. Today, copper sheathing has almost disappeared from use, being replaced by antifouling paints that contain copper or other additives to repel worms and shellfish.
In wooden boats, areas around the rudder, its bearings, and the rudder post and cove ahead of the rudder all provide hiding places for teredo navalis, the naval shipworm, and other marine organisms. It’s also difficult to paint in these areas. So, for maximum protection, we chose to revert to the centuries old, tried and trusted method of copper sheathing.
During the week, Wada was stripping the years of paint off the engraving that will be prominently visible at the bow and stern, at the start and finish of Cynara’s cove line. This same design will be traced and re-engraved on the newly restored knights head chocks on the top part of stem.
John was working on the fore-deck. Here, the base of the anchor windlass (which weighs 300 kilograms) must be incredibly strong. The windlass will have to haul in an anchor weighing close to 200 kilos, along with some 50 meters of heavy chain and hundreds of meters of wet rope. When an anchor bites on a hard bottom, the load on the windlass can be even more immense. Obviously, strength calculations are critical here.
Mattis and Richard were measuring lengths and re-cutting screw threads for fitting other small bronze parts to the deck. To match the depth of each hole perfectly, he needed to shorten the length of many of the bolts. These carpenters rely heavily on the feeling through their fingertips of each detailed part and angle. The skin of their fingertips becomes callused and crisscrossed with scar tissue, evidence the owner is a skilled artisan.
Friday, Ben was carefully checking the position and angle of a ventilator pipe before drilling a hole in the teak deck planking. Mistakes cannot be rectified once drilling has begun, so he was being very cautious. Of course, that’s true of all the steps being done now, as it’s mostly finishing work.
Thanks to all our readers for supporting us, and Cynara, over the year 2019. We look forward to sharing the events of 2020 with you as well!
Wada strips paint from the floral design at the bow to reveal lost detail.
The gloss varnish of the stern section is looking particularly beautiful.
Preparation for another coat of varnish.
The view from this porthole will dramatically change once Cynara is back sailing again.