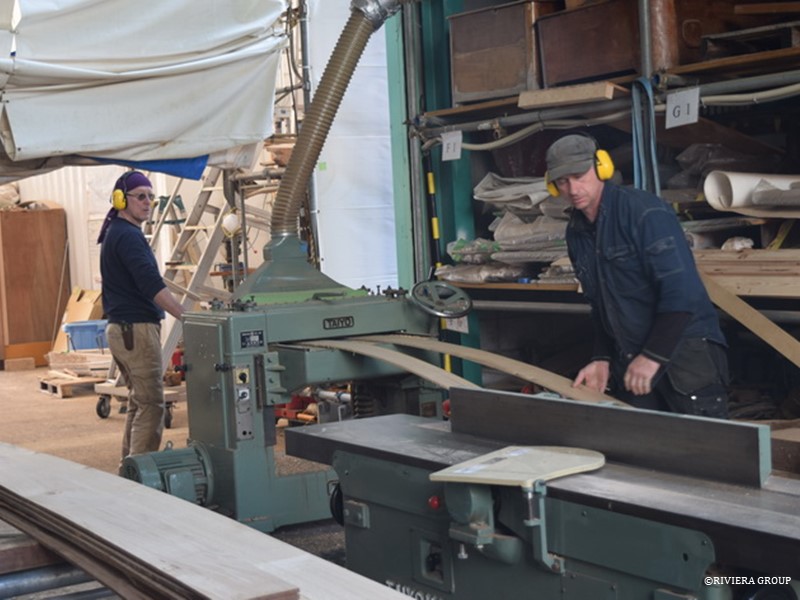
Blog — March 26-30, 2018
Once the deck beam laminates were sufficiently dry, they could be machined to size before being set aside to rest the exposed fresh timber. These (above) are almost ready to laminate. The laminates have to be dry before final machining to get them within the glue tolerances.
Producing the first futtocks took time, but Nico now has the process down to an art, and they take shape quickly.
Lewis makes a plywood pattern to check the frame against the ribbands.
A final check of the alloy plate (above) before the rebate is cut in the backs of the frames (below).
The plate is bedded in on copious amounts of red lead putty that we made onsite from raw ingredients.
The site of Kawashima’s keel repair is ready for glue. The strange shape is due to its location adjacent to the scarph joint in the keel timber. We didn’t want to blue a patch over the joint.
The lower edge of the keel timber had some damage from previous attempts to stop leaking with caulking. One or two areas needed to be cut out, and fresh timber was inserted.
Repairing a damaged edge prior to refitting the garboard strake.