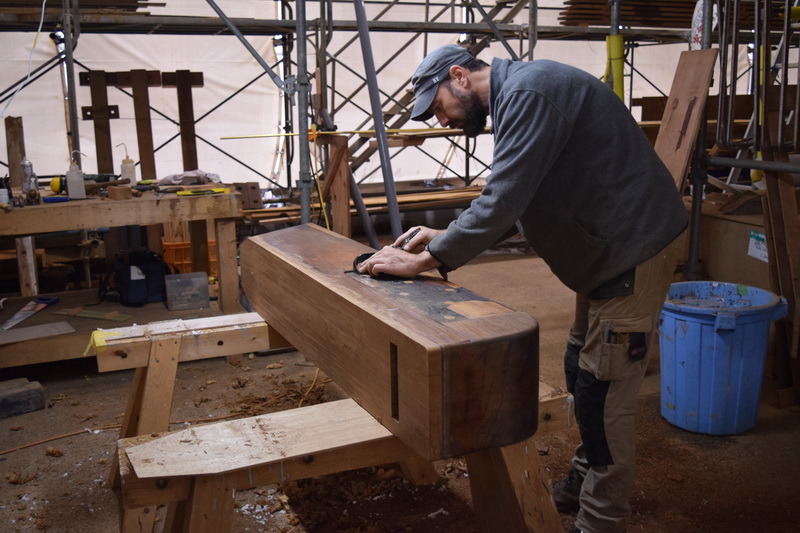
Blog — Wednesday , 30 October, 2019
Tues. Oct. 22
With the deck planking done, we have the entire deck as a workspace. Nico is working on the bowsprit chock, and can now put in temporary place to make sure it fits. It is a sizable piece of wood and is all original.
Further back, Richard is drilling and setting out deck fittings in the coverboard.
Wed., Oct. 23
Tatsumi and Kawashima are working on the wall partitions for the interior. The wood is poplar, not often used in Japan. Paul says he chose this because it works well for painted surfaces, and because Camper and Nicholsons, who built the boat in 1927, used it in the original.
Thurs. Oct. 24
Richard, the engineer, is in his element in the engine room, and he can get possessive over his responsibilities (“This is my room,” he jokes.) It’s partly true: there is more engineering than woodwork since everything—metal tables for the generators, the engine, pumps, etc.—all have to be set up correctly for the engine to be easy to use and maintain in a limited space.
Wed. Oct .30
Richard the carpenter’s next step on board is to cut the top of the wooden stanchions down to the correct height (above) while another Japanese team member sands the coverboard, preparing for the first coat of varnish (below).
Wada has taken a central role in the varnishing of the masts, which have become much darker in tone after many coats. It is a repetitive job that requires a lot of concentration.