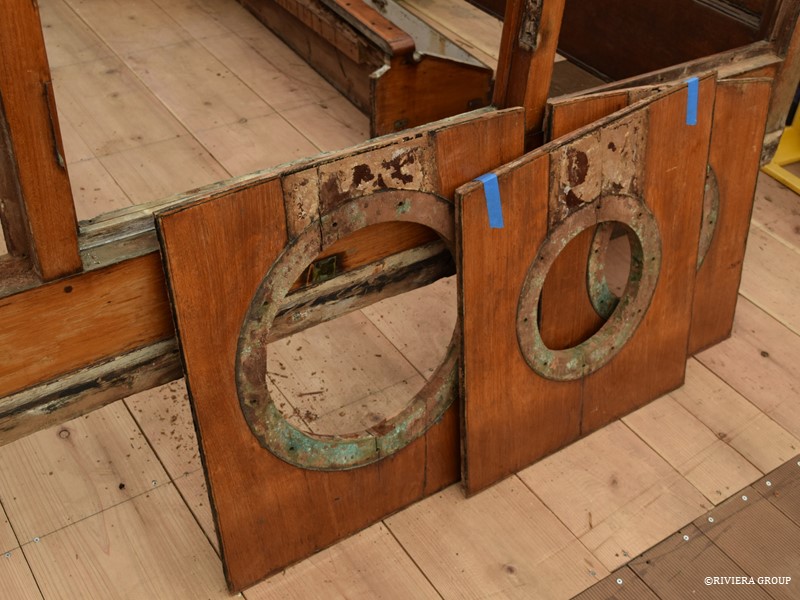
Blog — May 21-27 , 2018
May 21 to May 27, 2018
The deck house panels with the portholes have been removed, revealing more information on their past. We’re still investigating the deck house’s original appearance.
It’s time to give the new stem it’s first dry fit, to fill the gaping hole where the old one was removed.
It still needs the bevels and the boxes cut for the frame ends, but we needed to check if the overall shape was on track.
The hood ends (above) had to be prized apart to fit the stem into position.
The back section of the stem fits well. It still needs a nosing attached to complete the stem profile, but we were relieved to see how well it fits before going any further.
The stem is back on its frame and Ben is fine tuning the rolling bevel where the hood ends fit tightly against the stem.
Lewis Hockaday (above) and Nico Calderoni (below) work at one of the most complicated junctions on the boat. The top of the stern and the end of the horn timber is where the hull transitions into the rudder and continues out to create the counter. There are many curves converging here, and the futtocks are particularly difficult to fit.