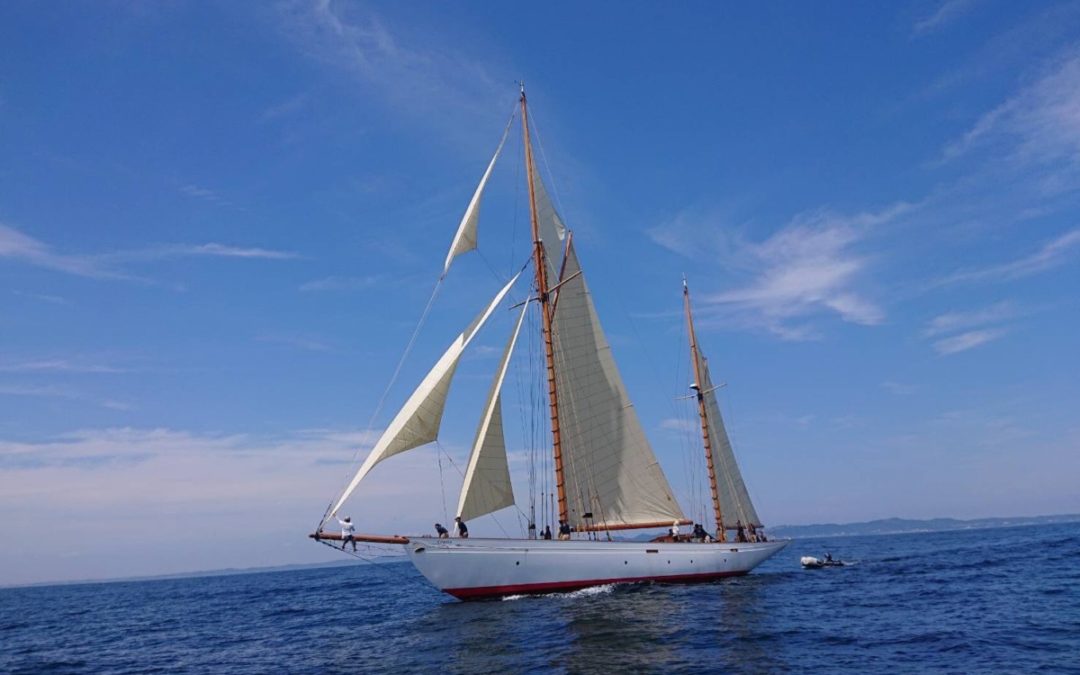
Blog — Tuesday , 23 June, 2020
Tuesday, June 9
The day started early, with Paul gathering all the Japanese craftsmen for a progress meeting (below). He covered all the various tasks that need to be done, and made a schedule leading up to the launching ceremony.
Murata applies varnish to the mizzen boom crutch (top and above). The leather, where the boom will rest, is covered in leather, stretched to shape and held with copper tacks.
Kakimoto fits the boxes that go between the deck beams and cover the tops of door frames and panels. The boxes look like continuations of the deck beams, and are a convenient space to hide wiring.
Massa has been working in the galley but the galley will have to wait as he turns his attention to the bathroom unit tops.
Kawashima fits a false beam in the main saloon. This serves the same function as the other boxes fitted between beams (see above) except this one runs across the ship instead of fore and aft. You can see the wiring that will eventually be hidden in the false beam.
Monday, June 15
Today was the first of many sail tests and full-scale training runs for the new Japanese crew. Under the guidance of Chuck and Nat, Shindori, Yokokawa, Saito, Tanaka, Fujita, Kawashima, Murata, and Pascal boarded for training. In the morning, it was extremely hot and almost windless, but as the sails went up afternoon, a good breeze picked up and Cynara began her first sailing voyage in many years. The wind was perfect and Chuck kept her on a straight course at first; for a while it seemed they would cross Sagami Bay. Then they turned back and returned to the marina in the late afternoon. Chuck was very pleased with the training.
Wednesday, June 17
The galley worktop takes shape. The space for the stove is almost ready to fit the stainless steel lining which will make keeping the area clean, easy and practical. The galley worktop is made in African mahogany but the cupboard fronts are in Honduras to match the guest areas.
The original pantry that was here before would have been very plain. But modern galleys are often used by owners and guests and so need to be of a similar quality to the rest of the guest areas.
A touch screen is fitted on the galley wall next to the door leading to the guest accommodations. This will allow the crew to monitor the ships systems, air conditioning and lighting without disturbing guests.
Friday, June 19
It rained all day today from morning, so it’s good to still have the tent for use as a workshop. John applies shellac to one of the fixed dressing seats that will be in the staterooms. The panels are ventilated as air conditioning units will be placed inside. These are all made in solid mahogany and traditionally joined.
Tuesday, June 23
Shingo and Murata are applying Danish oil to the hull ceiling in the crew quarters area. This “ceiling” is planking that goes against the inside of the frames, sealing off the interior from the hull. It was first used in the tea clippers that brought tea from China, to keep their precious cargo dry. Any moisture that makes it through the hull is stopped in its tracks by this “second skin.”
Work is continuing on the washbasins . . .
. . . and the saloon. Pascal and Ian are working on an A/C unit that is concealed inside the main saloon couch.