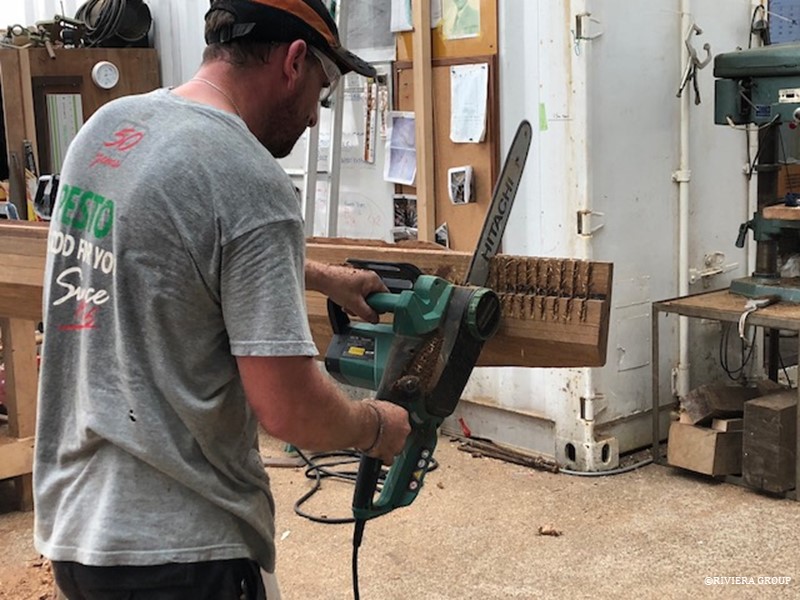
Blog — July 23-29 , 2018
July 2018 , 23-29
Ben kerfs the stem with a chainsaw (above). This is part of the nosing, the second part of the stem repair, which will create the point and leading edge that is seen on the outside of the stem forward of the plank ends. Kerfing, which is cutting a series of slots across the grain, allows for the faster removal of unwanted sections, and reduces the risk of tearing into the wood that needs to be retained. A slip (a large chisel) is used to remove the excess material (below).
Test fitting the final stem section.
Lewis helps Mattis and Richard drill the holes through the planks, frames and floors so that the large copper rivets can be fitted, permanently fastening the floors in place
Richard peins over the heads of the rivets inside the hull. The floors are bedded in red lead putty.