June 11 to June 17 , 2018
As soon as the yacht was lifted from the water, we noticed that something strange had happened to the after end of the ballast keel. The usual method to connect the ballast to any deadwood or false keels is a large scarph joint securely bolted. And that’s what was shown on the Camper and Nicholsons drawing. But what was there was a butt joint with a small timber tenon.
After some research, a footnote on a drawing from 1928 showed that shortly after launch, the scarph joint was cut off and just under a ton of lead removed. This points to the possibility of a rare error in C&N’s drawing office. Calculating the water line on large vessels without the aid of CAD was nightmarishly difficult, and all the calculations of mass, volume, buoyancy, center of gravity, etc. had to be done with slide rules and old-fashioned math. Small errors were inevitable, and the reason why boats carried internal ballast that could be moved around to trim and balance the boat.
Clearly, Cynara was a little heavy in the stern and so the solution was to lose the end of the ballast. We had two options: make the keel shorter by recutting the scarph or leave as is. We chose the second option, though we did reinforce the joint with large bronze dovetailed plates on both sides.
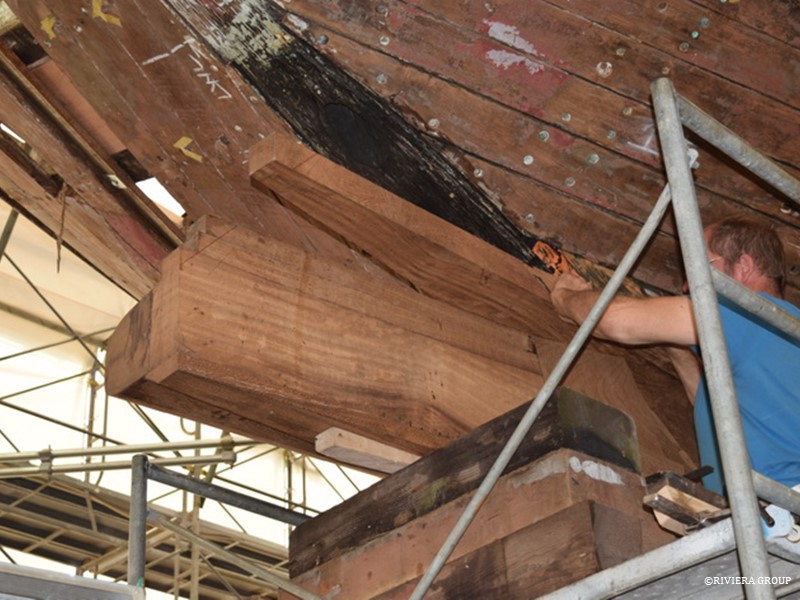
Lewis is dry fitting the shaft log and checking his measurements (above and below).
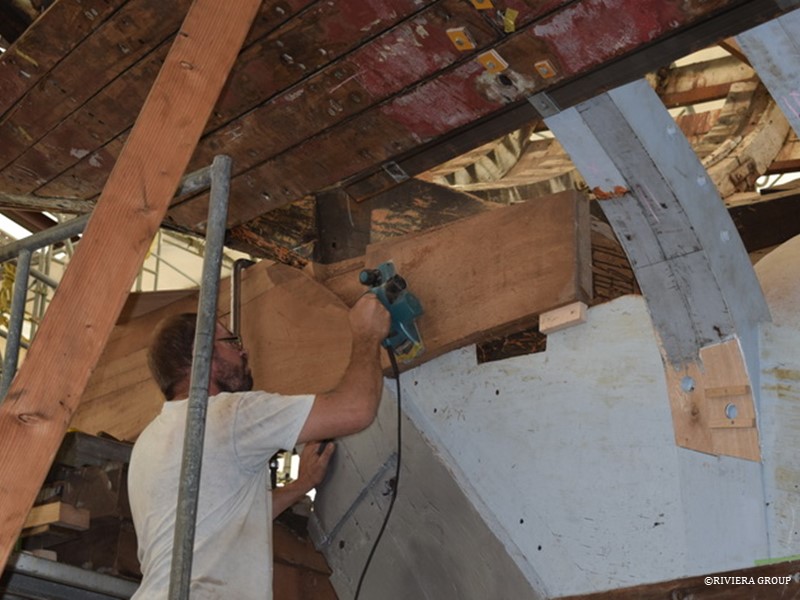
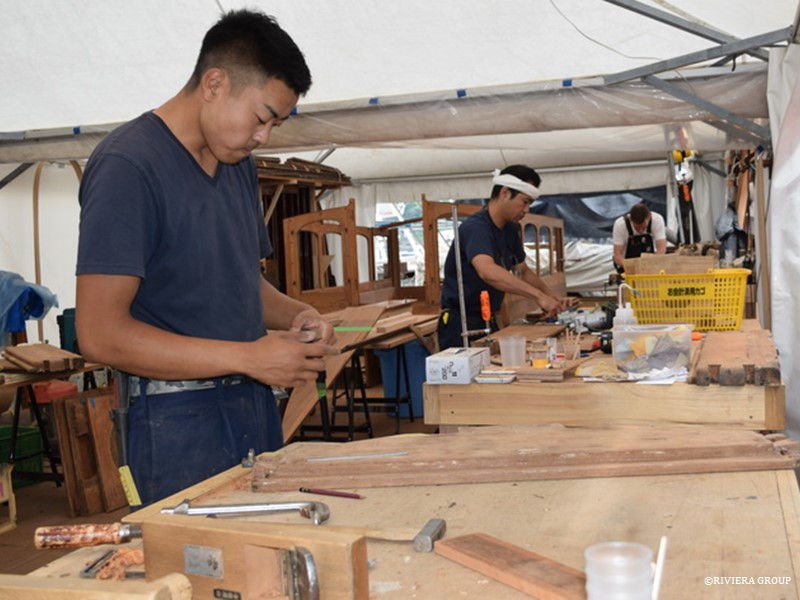
Meanwhile in the joinery tent, the deck furniture repairs (above and below) are moving quickly as the Japanese joiners have become more familiar with the construction style of a traditionally built European yacht.
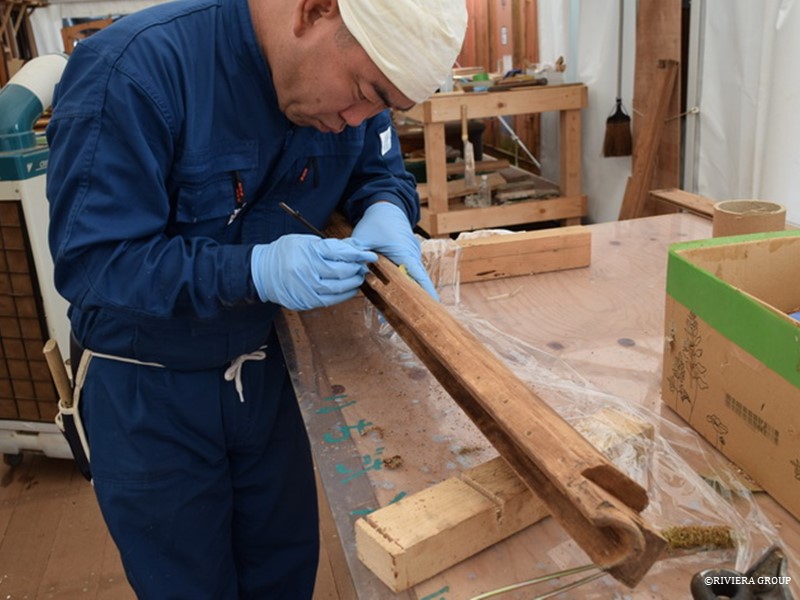

The main deck house is now looking healthier after years of varnish and paint have been stripped away.
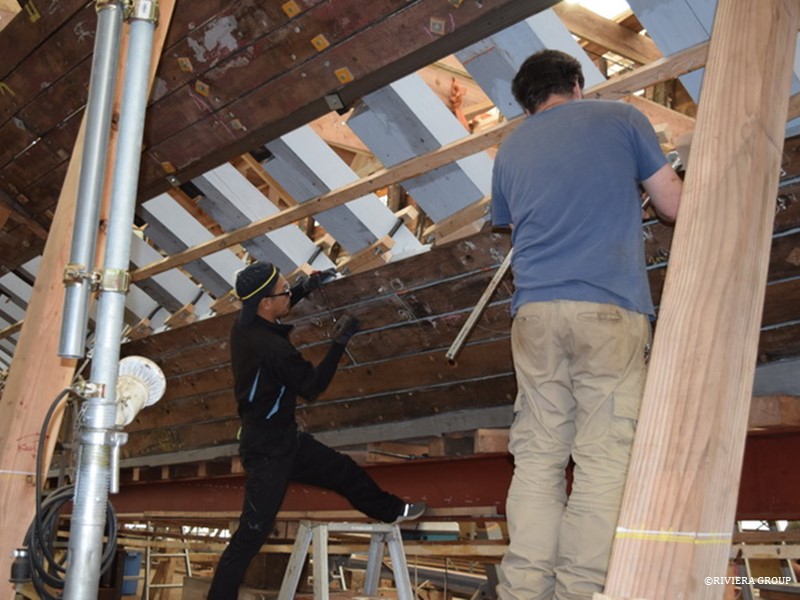
Paul helps guide in the first fit of the new engine room bulkhead (upper right) as Nico completes the installation of another strake.
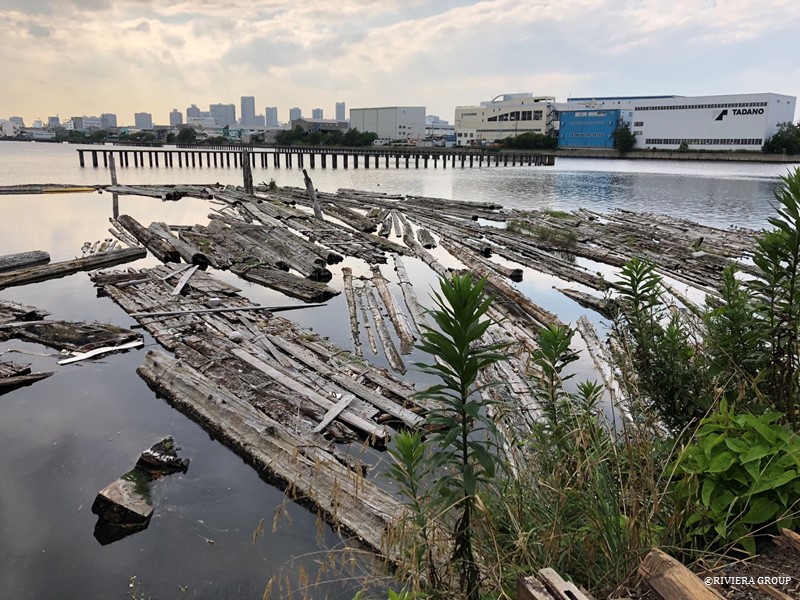
The search for teak to replace parts that are not salvageable continued. We even visited a lumber yard in Tokyo’s Kiba area, the old timber district, and were able to find some of what we needed. In pre-modern times, the cargo of lumber would just be dumped in the river and then hauled up with chains to be sawn. Most today comes by truck, but some can still be seen floating outside the yard (above). They told us that more was at the river bottom. “There’s still some good stuff down there,” they said, “but you’d need divers.”
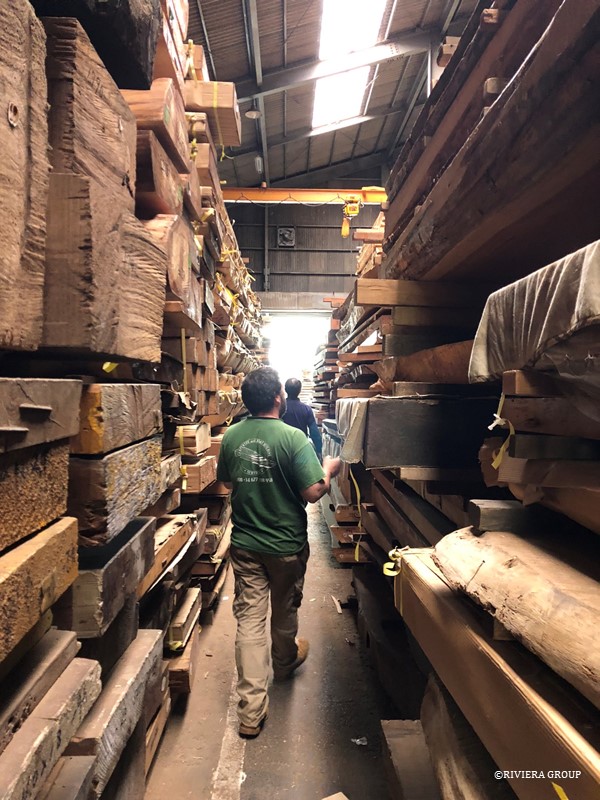
We decided to pass on the underwater search and focus on the stacks in the warehouses (above). We were able to find some pieces that were on our list of needed timber.
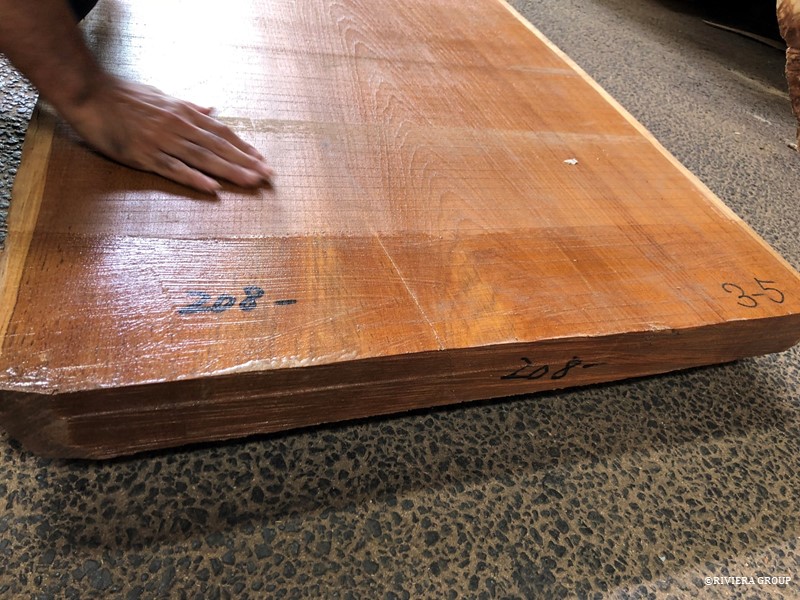

More views of the trial fitting of the new engine room bulkhead (above and below) before it is galvanized.
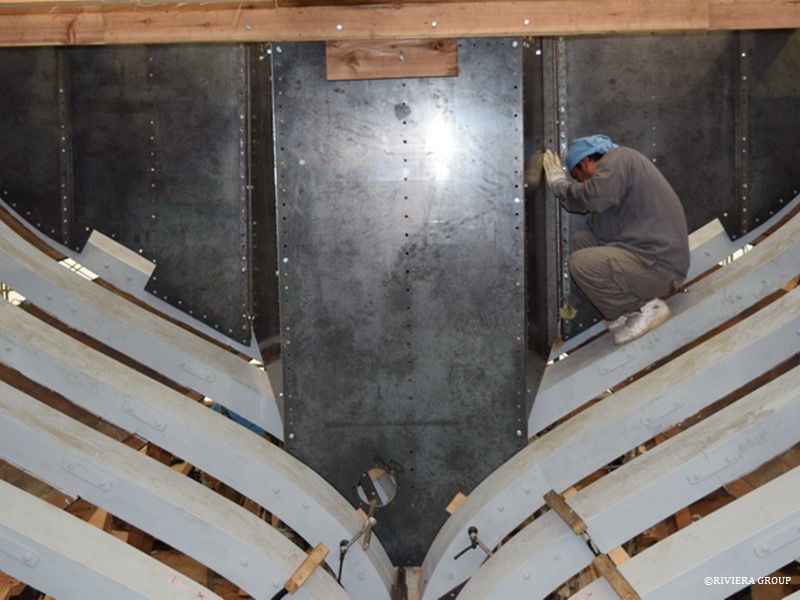