April, 2018
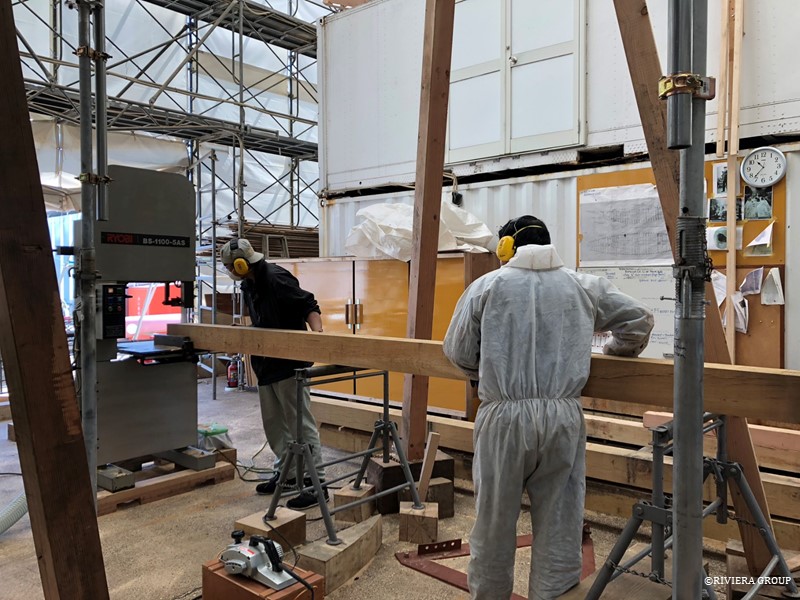
The laminates for the deck beams are being rough cut on our bandsaw (above). The timber is heavy and awkward to manipulate even after it is resawn into manageable sizes.
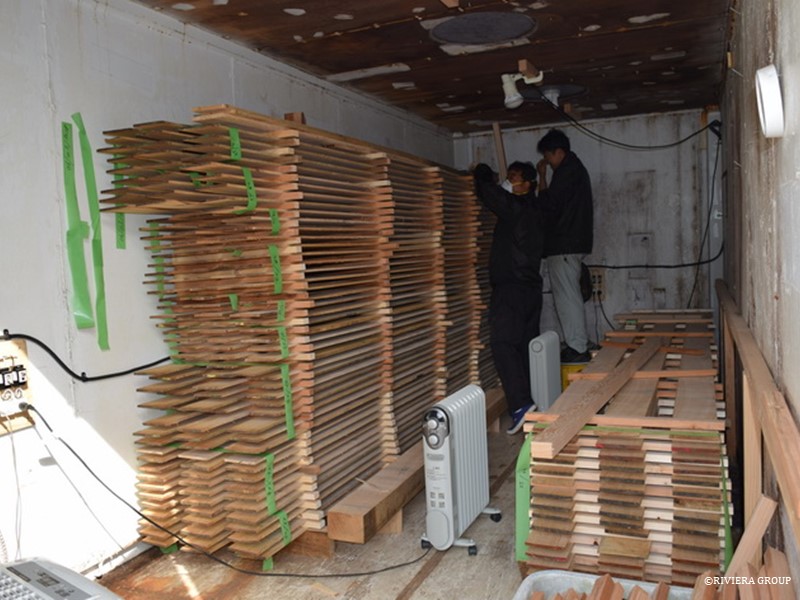
The laminates are stacked in our drying shed.
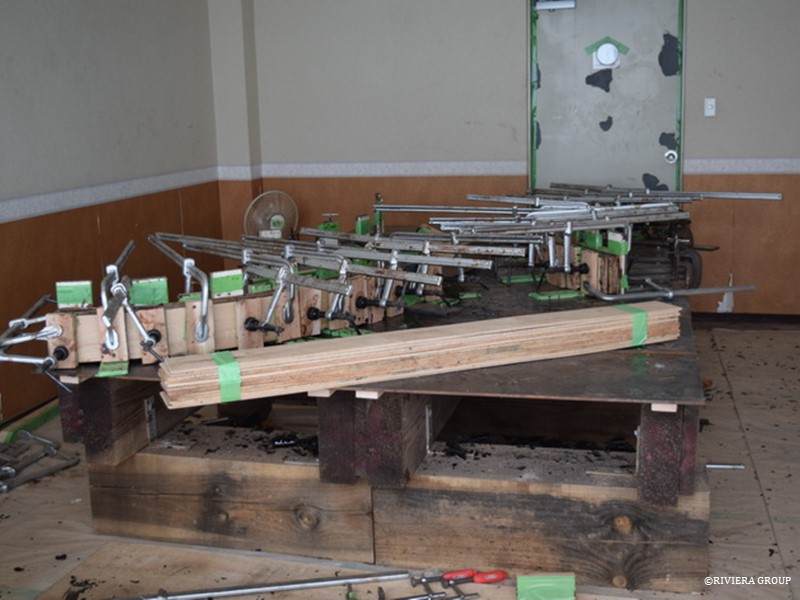
A very few of the futtocks have too much shape for our oak stock, so they have to be laminated to accommodate the curves.
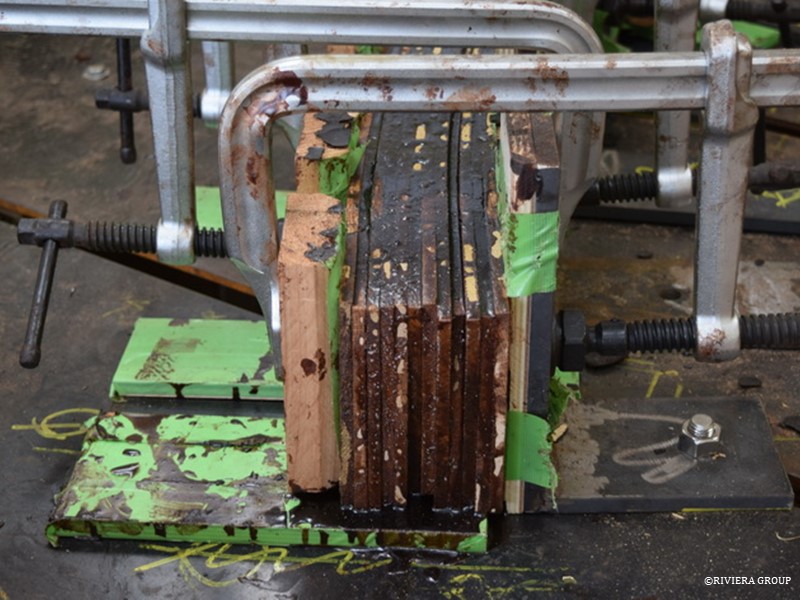
For the laminating, we use resorcinol glue, a formaldehyde-based glue introduced in the early 1940s. It has better UV and heat resistance than epoxies. While epoxy has been the “go to” glue in recent decades it is not always the best choice. We went with resorcinol because oak, with its high acidic and tannin content, resists epoxies. It is interesting to note that no glue was used when Cynara was constructed at Camper and Nicholson’s Gosport yard. Sealants made from tars, oils and lead compounds were used, along with various time-tested joinery and shipbuilding techniques to keep the components together (along with a lot of rivets, etc.) Glue is no substitute for good joinery, so we keep the use of glue to a minimum and use the same joinery techniques as when she was built. But glue does give us options, such as the laminated deck beams or plank repairs.
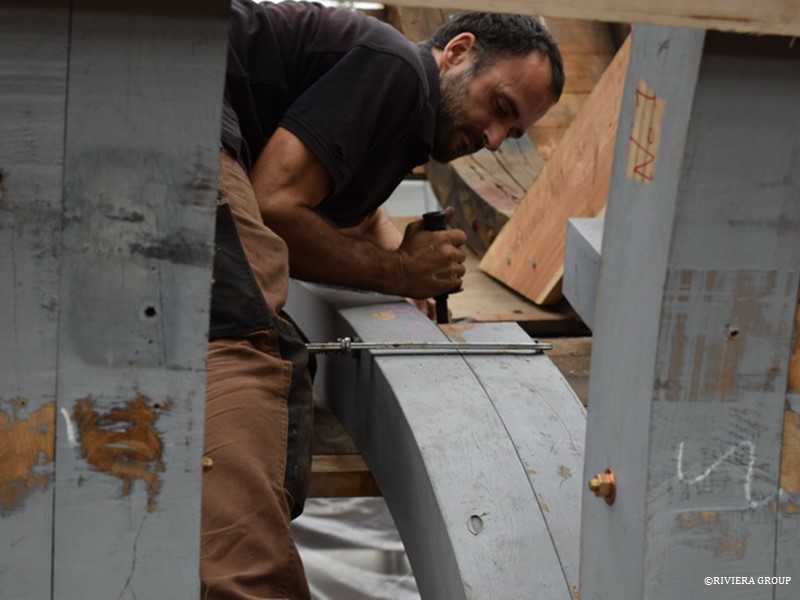
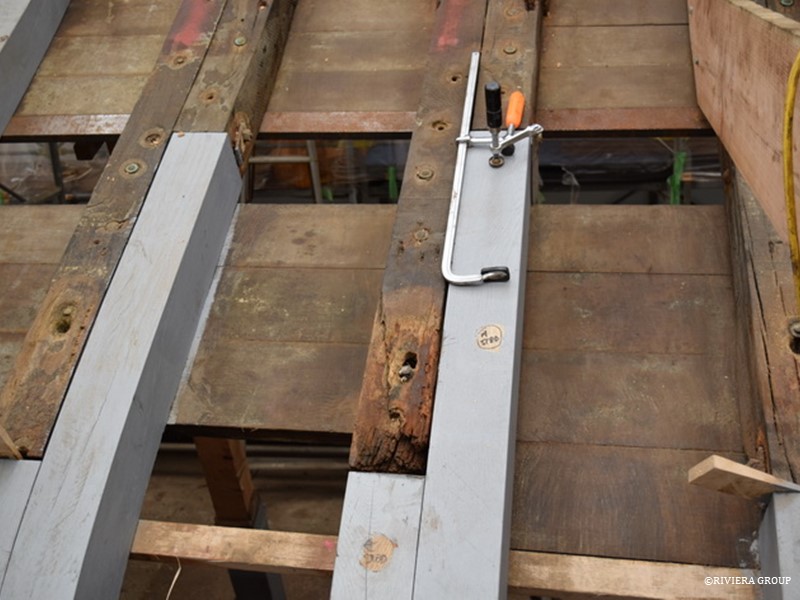
Now that the keel is straight and the lower frame pairs are fitted, frame replacement can move up the hull (above).
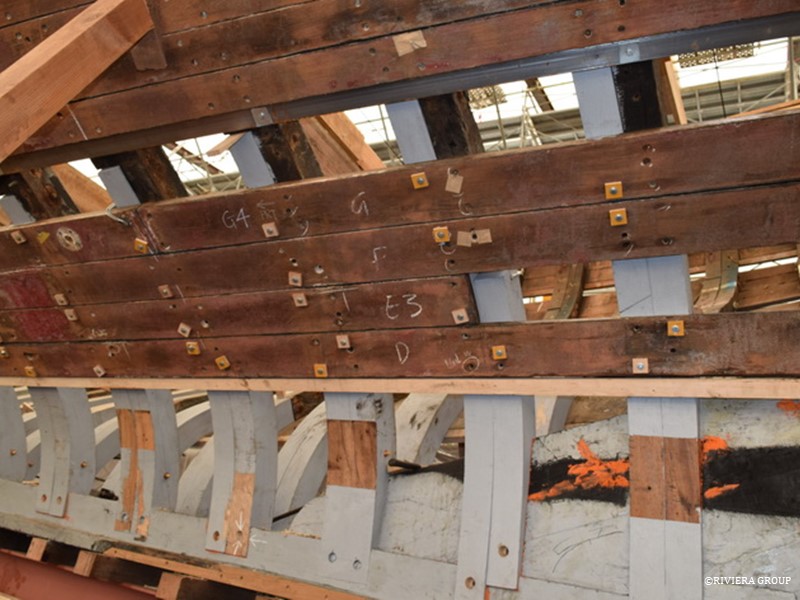
The frames are held against the old planking with temporary fasteners and the shape of the hull is constantly monitored.
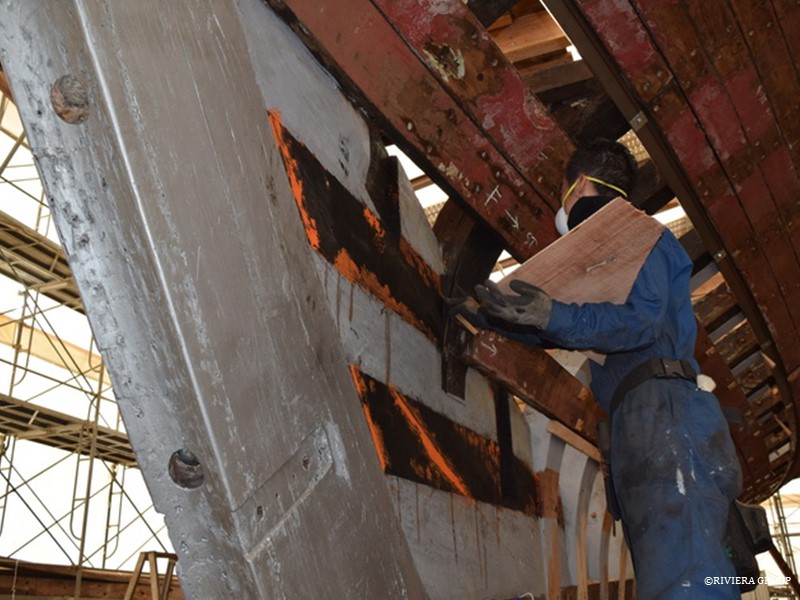
The stern post and stern knee are painted with an underwater primer, and gaps, frayed surfaces, etc., are treated with liberal amounts of linseed oil and red lead. Even after these precautions are taken, the saturated timber moves as it dries—we just hope to slow the process until it is encapsulated with fresh timber and new bolts to hold it. Red lead putty is used because it dries slowly, and it will not have an adverse effect when the timber swells again. Using hard compounds like polyester resins or thickened epoxy would harden in the cracks and act like wedges as the timber swells, potentially expanding the cracks even further. A soft compound is needed, so we use the linseed oil putty with plenty of red lead powder. The paint will most be lost during the fairing process later on.
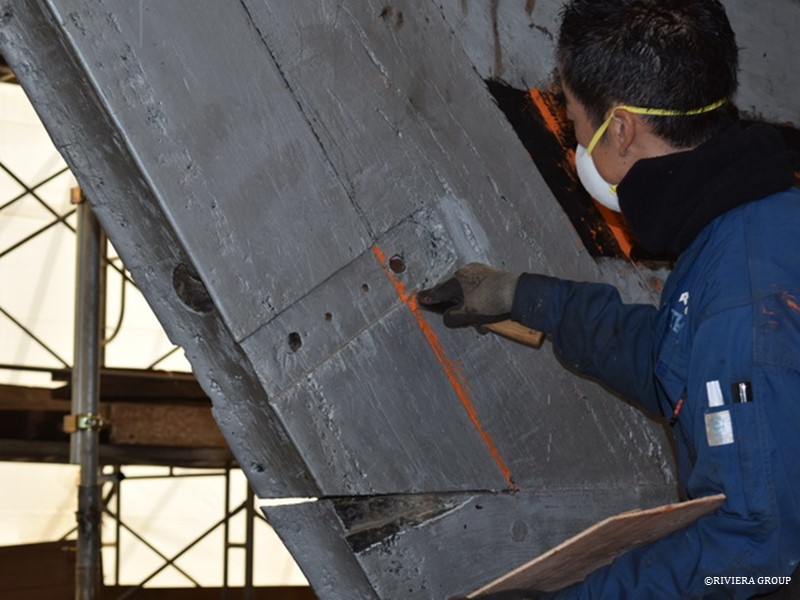
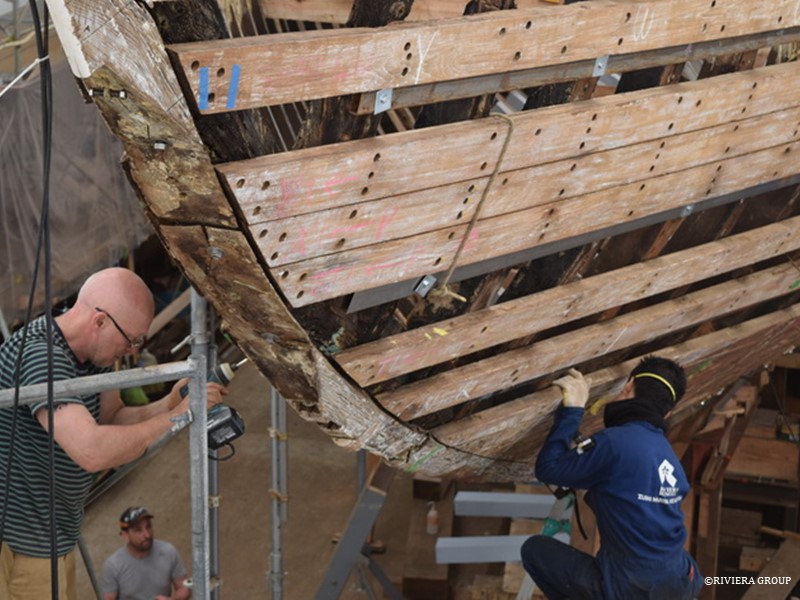
Preparing the stem for removal (above), and after it has been lowered to the floor (below).
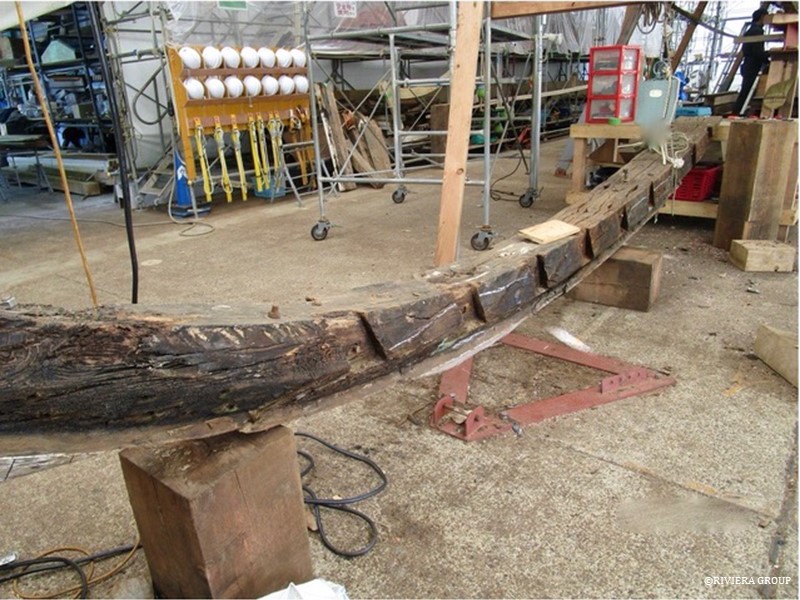
Unfortunately, after the planking was released and the stem was revealed in its entirety, large cracks were appartent behind the plank ends and the centerline. There was also significant fresh water ingress at the top of the timber. There was a previous repair that replaced the stem head and the lower half of the stem had also been previously replaced. It was also significantly distorted, meaning the boat would always have a “bent nose.” We decided to remove it and replace it so as not to disrupt other work. It was a tough decision to make but . . .

The heavy oak stem section was moved to the joinery tent where the new section would be made.
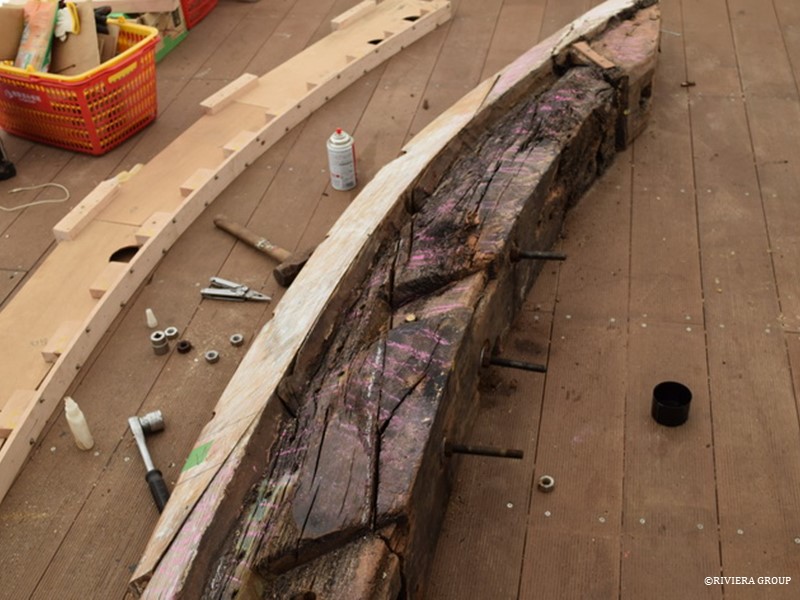
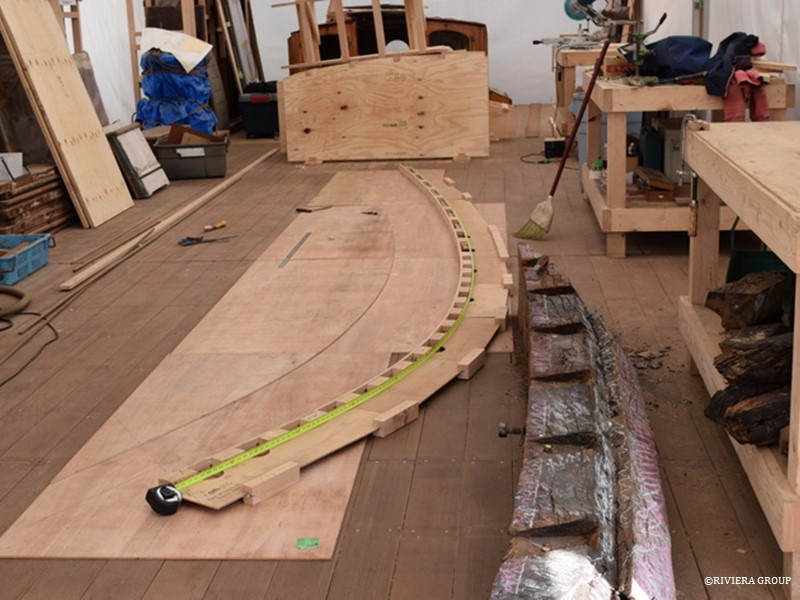
The stem issue had not been anticipated, and such a large and complicated part could not be produced from our oak stock. The long sweeping curve would have to be cut from equally curved wood, hand selected from a whole oak tree. Instead, this was going to have to be laminated in locally sourced timber. The lower section that had previously been replaced had been done in iroko and this seemed like a sensible choice. Iroko would be equally strong, if not stronger as the laminations would follow the long curve and leave no short grain. The stem was drawn full size on the joinery floor and a jig was built to bend the laminates over during the gluing process.
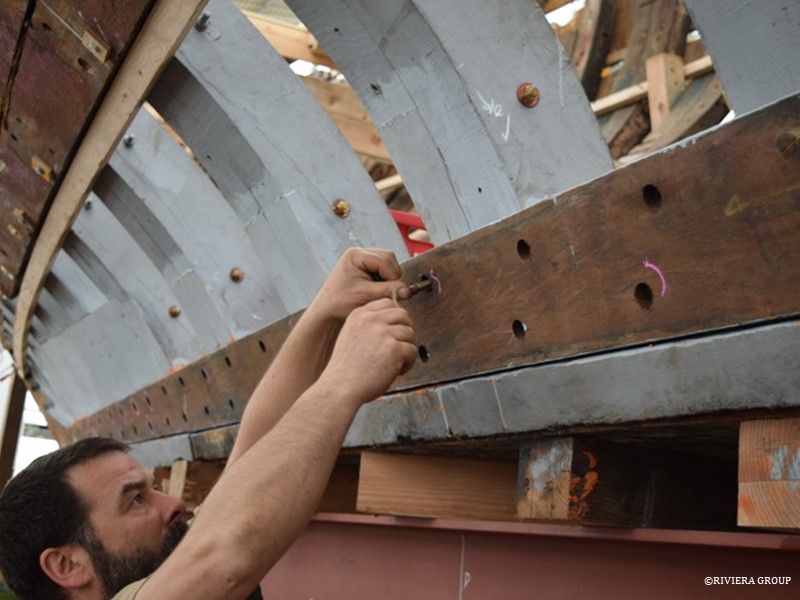
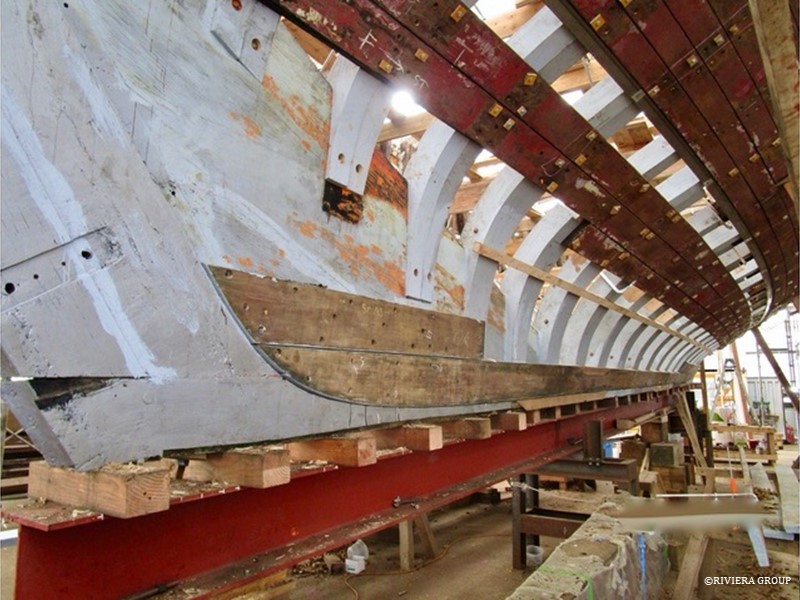
Now that all the lower frame pairs had been fitted and fastened we were in a position to fit the original garboard strakes. The individual planks had been cleaned and repaired it was a good sight to see them refitted and bedded in copious amounts of red lead putty, locking all the frame ends in place.
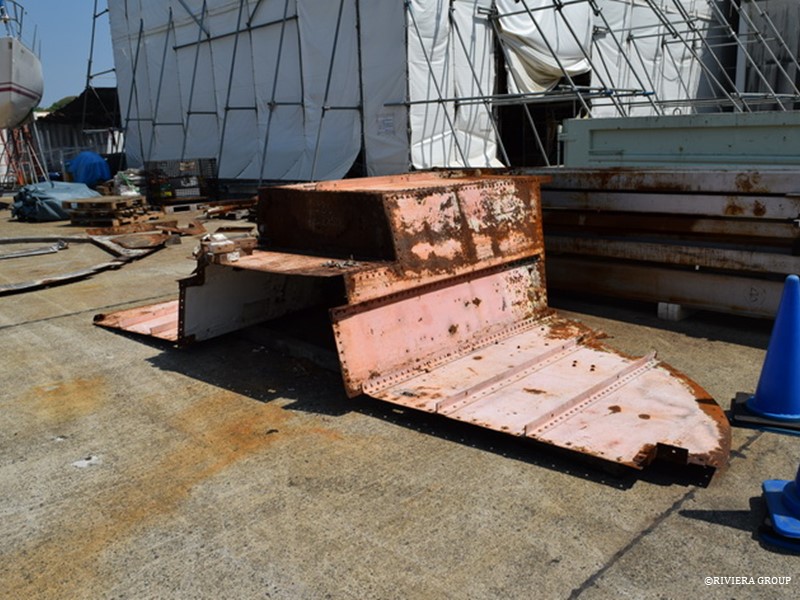
The engine room bulkhead was sand blasted by Sawamura, who was concerned by its condition. Paul thought that much of it could be retained, with the bad parts removed and cut away in sections with new parts welded. Sawamura preferred to replace the whole bulkhead and after the cost was calculated to be the same, that was the final decision. Sometimes authenticity has to be sacrificed, but building a new one would not be simple. . . .
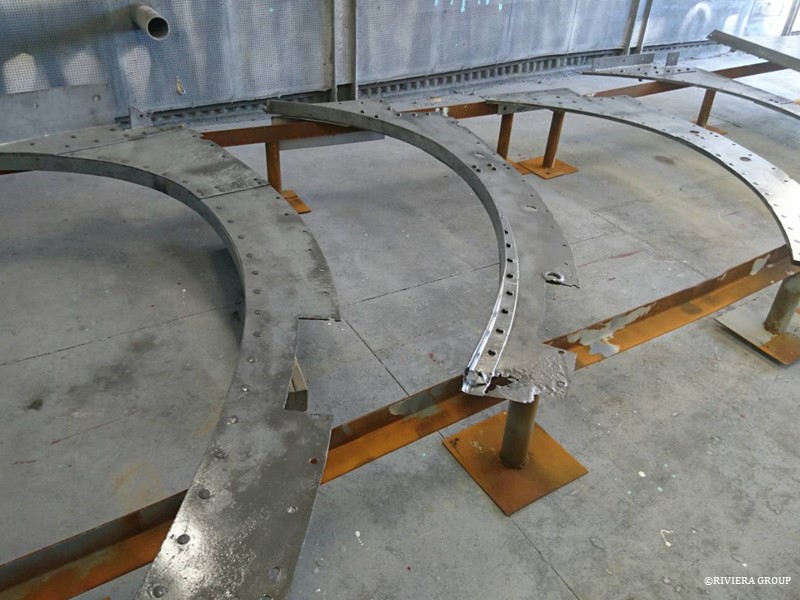
The web frames that are situated at the main mast and just after the main mast (above) were also sandblasted along with the floors and knees (below) that were good enough to reuse.
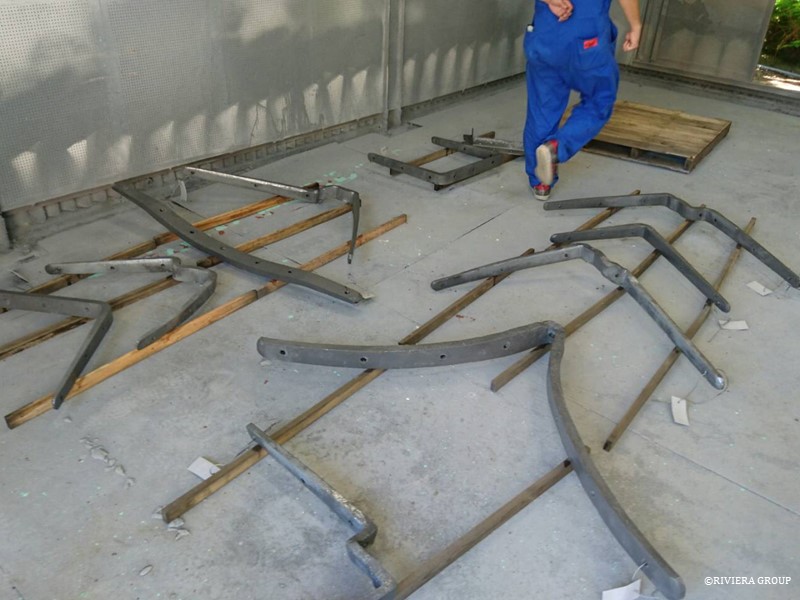
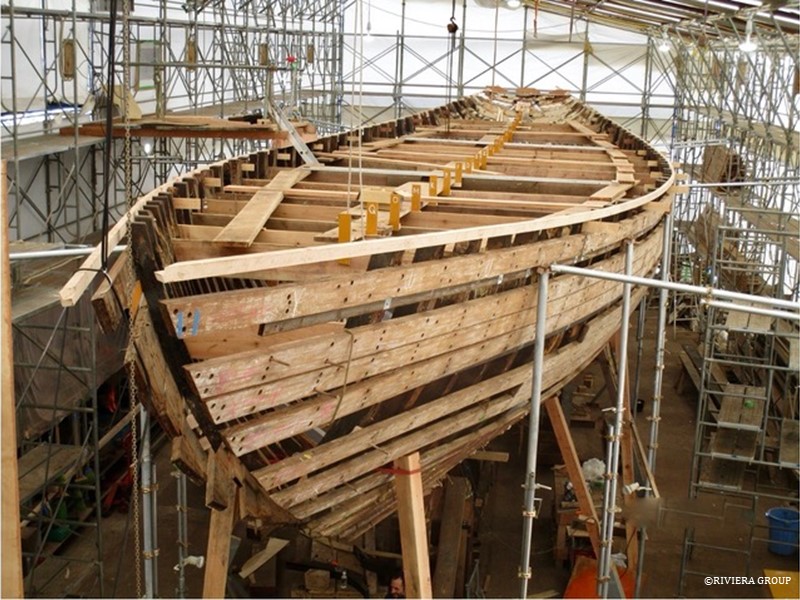
With the stem removed, Cynara was looking very fragile.