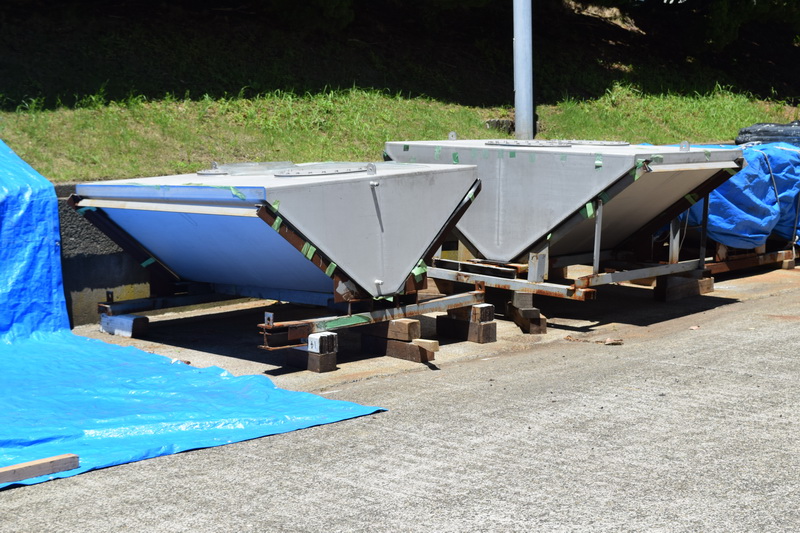
Blog — Friday , 21 June, 2019
Monday, June 17, 2019
The tanks have been fabricated of stainless steel and pressure tested. Now they’re ready for installation.
Hashimoto has begun production of the circular surround for the sail locker hatch (all the other hatches are square). The plan (below) shows its location.
And work is continuing on the pattern for the coverboard that will show the shape, the joint positions, and the stanchion positions.
Tuesday, June 18, 2019
Three craftsmen from Stirling & Sons have been fairing the hull to make the surface perfect.
Ben and Richard continue to work on the placement of the tanks and engine.
General repairs are continuing in the workshop . . .
. . . on the circular sail locker hatch . . .
. . . and repairing original hatches where old fittings have allowed fresh water ingress.
Chuck and Nat have set up their workshop for working on the mast.
Wednesday, June 19, 2019
This primer coat helps in the hull fairing process. When the hull is bare timber, only the most obvious imperfections can be seen. But with the uniform color of the paint, more detail is visible. The hull is then sanded with long boards (long, flexible sanding boards made of plywood), which remove the paint from high spots—showing where sanding is needed.
Wada and Kakimoto started painting the sail locker in the interior of the stern, seen in the plan above. This is used for the storage of sails, lines, deck gear tools and spares.
The three men from Stirling & Sons are using long boards as they continue to fair the hull.
Thursday, June 20, 2019
As Ian sands, the high spots appear as the wood shows through the paint. As the hull becomes fair, most of the paint will be removed.
Samples of the refurbished original lights and door handles have arrived back from the UK. One of the old ones can be seen in the background of the top photo. The patterns all date from Cynara’s original build in 1927.
Friday, June 21, 2019
Nat sanding the masts.
The sub-deck part of the coverboard is ready to install at the base of the stanchions. Things have really picked up with all the various work going on around the yard,