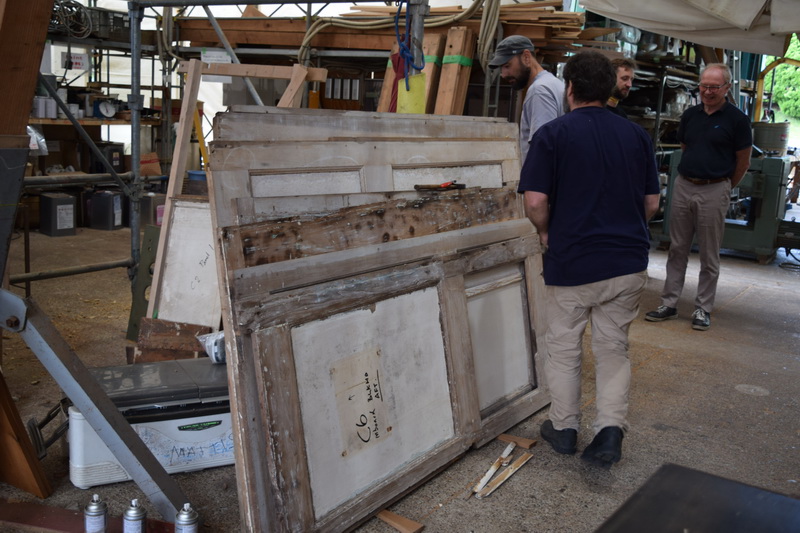
Blog — Monday , 23 September, 2019
Thursday, September 19, 2019
Full-scale restoration of interior fittings has begun. Currently, we have completed some of the procurement of the needed wood material, but we’ll need to make further wood purchases as we discover what is usable and what is necessary.
The king plank that makes up the center line is finished. Once this is done, the rest of the planks will be set working from the outside toward the center. The team consists of six members: a teak processing team and a deck surface team.
Friday, September 20, 2019
Teak planks are laid out, graded and checked for faults.
To avoid too many butt joints on deck some of the teak was joined using scarf joints.
Now that the finish is in sight, things on deck are moving quickly. The planks are carefully marked with whether they are for the port or starboard side and the length. This is the eighth day since the deck laying team has started work, and they want to finish in order to catch flights out of Japan on October 26.
Monday, September 23
The heat has returned along with a strong humid wind thanks to Typhoon Hagibis, and work on the deck planking is starting to pick up.
Hutchets or oversized washers are used to pull the planks down into the glue. We use 5mm aluminium bar to make the hutchets which is also conveniently the same size as the plank seams. This means we can also use the hutchets as spacers between planks. The planks already had the 5mm seam machined on one side but sometimes a spacer is needed.
Our “Italian team” of Niko and Carlo is focused on the interior partitions. We have CAD drawings, but as this is a wooden ship the dimensions in the drawings and those in reality still need to be checked against each other. This also allows us to make changes, if necessary, if the drawings do not have some of the detail we need included, such as pipe runs and wiring. The galley mock up above was measured and the real galley is being made by Masa (and the team) onsite.